深度报道 | 绿色鞍钢是如何炼成的
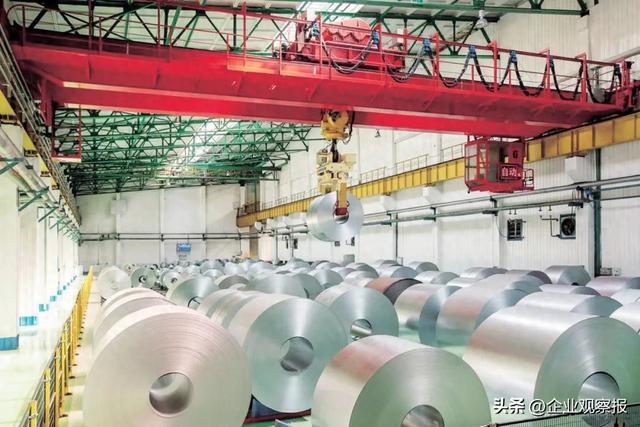
绿色化是现代产业体系的基本特征之一,钢铁行业作为典型的资源和能源密集型产业,能源消费总量约占全国能源消费总量的11%,碳排放量约占全国碳排放总量的15%,是节能减排的“主战场”。
在国家“双碳”战略指引下,推动钢铁产业绿色化转型,是钢铁行业高质量发展的内在要求。
作为中央直管的国有大型企业,有“共和国钢铁工业长子”之称的鞍钢集团,近年来成为央企践行ESG、加速绿色低碳转型的标杆。
“2022年,鞍钢集团吨钢碳排放量比2000年下降约1.5%,成为助力全球生态文明建设的重要力量。”鞍钢集团董事长、党委书记谭成旭说。
近年来,鞍钢集团坚持打造绿色鞍钢,把绿色低碳转型作为驱动高质量发展的重要引擎。鞍钢自主建成了全球最大的铁前一体化智慧炼铁中心,掌握了拥有完全自主知识产权的全球首套绿氢零碳流化床高效炼铁新技术,“基于低碱高硅球团的低碳排放高炉炉料解决方案及其应用”获得了世界钢铁协会低碳生产卓越成就奖。
“十三五”以来,鞍钢集团绿色低碳发展指标持续提升。2022年,吨钢综合能耗、吨钢耗新水分别同比降低1.49%、5.35%;二氧化硫、氮氧化物、烟(粉)尘排放量分别同比降低14%、10%、12%;COD、氨氮排放量分别同比降低30%、14%。均实现历史最好水平。
2022年,鞍钢集团营业总收入3366.16亿元,利润总额80.14亿元;粗钢产能达到6300万吨,鞍本重组后粗钢产量在辽宁省占比58.60%;铁精矿产量持续保持国内第一、位居世界第五,成为推动东北振兴与保障国家战略资源安全的中坚力量。
2023年,鞍钢集团在世界500强中排名第283位。
鞍钢集团强化顶层设计,统筹考虑各基地现状,协同推进降碳、减污、扩绿、增长,将系统观念贯穿“双碳”工作全过程,以数字化、智能化建设与研发低碳技术推动能源利用率、劳动生产率和系统能效持续提升,实现了绿色低碳发展与经济效益相统一,走出了一条具有鞍钢特色的绿色低碳高质量发展之路。
近日,企业观察报走进位于辽宁省鞍山市的鞍钢集团,深入鞍钢股份铁前一体化智慧炼铁中心、鞍钢股份冷轧厂彩涂分厂、鞍钢矿业关宝山公司“黑灯工厂”等一批绿色低碳智能工厂标杆示范项目调研采访,探寻鞍钢集团冶炼“绿钢”之道。
01
智能集成,实现全流程降碳
通过建设智能化集控中心,系统推进钢铁全流程降碳,是鞍钢集团绿色低碳转型的法宝之一。
走进鞍钢股份炼铁集中操控中心,可以看到整个鞍钢的铁前生产、高炉炼铁、铁水运输等流程及数据完全展现在操控中心的大屏上。大屏前,仅有几个操作人员在监控和操作。
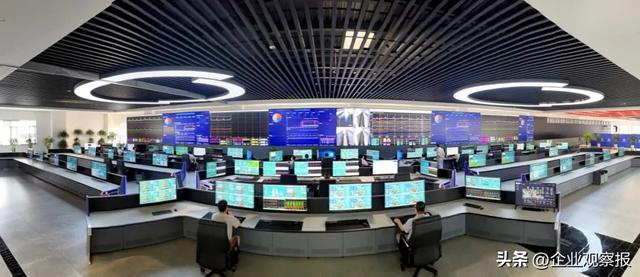
鞍钢股份智慧炼铁集控中心 ▲
这一集中操控平台就是2022年8月鞍钢集团自主建成的全球最大铁前一体化智慧炼铁中心。该平台集成了烧结、球团、焦化、高炉工序,融合了生产操控、设备监测、指挥决策以及工业大数据平台,是鞍钢集团建设数字鞍钢、创新鞍钢、绿色鞍钢的重点工程。
“鞍钢聚焦生产运营中的难点、痛点,设计了这个集数据采集、智能视频、智慧操控、数据可视化、智慧分析决策等系统于一体的智慧生产运营管理平台。”鞍钢集团党委宣传部部长聂振勇说,鞍钢铁前一体化智慧炼铁中心的创新之处在于,打破了传统工艺间的数据壁垒,通过汇聚高炉及辅助系统的生产数据和操控数据,将分布在厂区内的28个操作室、104套控制系统全部整合融合,实现了跨区域、跨工艺、跨界面;集中控制、集中调度、集中管理;“云”“智”“算”覆盖产线全流程;各岗位职能间横向联通、纵向融合,极大提高了生产效率和能源利用效率。
“该项目的成功投运,为鞍钢集团各大钢铁生产基地通过数字化赋能实现由经验性管理向数字化、精益化管理转变提供了示范,更为钢铁行业提供了可复制、应用性强、极具推广价值的智慧集控‘鞍钢模式’。”聂振勇说。
鞍钢股份炼钢总厂三分厂炼钢作业区的转炉前,并不见职工身影。此时,他们正在控制室里,运用鞍钢5G+智慧炼钢集控系统,通过电脑屏幕观察炉火的亮度和形状,判断炉渣情况,传统的炼钢操作,需要依据操作者的经验来判断炉内钢水的形成程度,以及产生炉渣的情况。这种“经验炼钢”的操作模式,学习时间长,不仅难以保证多批次产品质量统一,还具有一定的危险性。为了摆脱“经验炼钢”的操作瓶颈,鞍钢集团大力度开展“智慧炼钢”技术攻关,将炼钢过程交给计算机“算法”和相关设备,依靠动态模型实时计算钢水温度以及碳含量等数据,实现了全过程动态自动控制的“一键炼钢”。
正在现场操控该系统的一名鞍钢职工感受到了变化:“智慧炼钢系统给复杂的炼钢设备装上了‘眼睛’和‘大脑’,极大地提高了生产效率。”
鞍钢股份炼钢总厂三分厂连铸工序也建成了“连铸集控中心”,实现了RH一键式智能生产,满足超低碳钢脱碳要求,在外界环境动态变化下能够做到成分、温度命中率100%,达到行业领先水平。
经过多年建设,鞍钢集团已建成三类39套智慧管理信息系统,构建起全方位实时动态监管体系。鞍钢集团建成投运的鞍山钢铁本部、鲅鱼圈、朝阳能源集控中心项目,实现了能源系统实时数据分析、用量预警、预测调配,有效提升了能源利用效率和人力资源效率。
数据显示,通过打造智能化集控中心,鞍钢集团近年来实现了稳产高产与提质增效并行。鞍钢集团围绕“钢铁、矿山、钒钛”生产长流程管控,自下而上逐层开展智能装备、智能单元、智能产线、智能工厂及智能基地建设。截至目前,3D岗位机器换人率提升20%,产线自控化率提升4.7%,操作室集中化率提升18%,生产执行系统建设覆盖率提升18%,累计41条产线完成智能化改造。
02
模式创新,推进全面协同
统筹推动各子企业协同降碳,是鞍钢集团绿色低碳转型的创新路径。
为推动绿色低碳转型,鞍钢集团强化顶层设计,制定了《鞍钢集团碳达峰行动方案》,成立了由集团主要领导亲自挂帅的碳中和工作领导小组,确定了集团公司“双碳”工作的组织机构、工作原则和重点任务,并统筹考虑各基地现状水平,协同推进降碳、减污、扩绿、增长。
“鞍钢集团要通过数字化、智能化实现生产全面可控、业务全面协同、数据全面共享、模式全面创新。”鞍钢股份企业管理部副总经理朱大鹏表示,鞍钢集团已建成了钢铁产业一体化经营与制造管理系统,鞍钢股份鞍山、鲅鱼圈、朝阳、本钢板材、本钢北营等五个基地接续上线运行,通过打通采购、生产、质量、物流、销售等价值链各环节,实现一体化经营管控、多基地协同制造。
数据显示,一体化系统在本钢上线后,热轧热装率提高12%、在制品库存降幅21%、吨钢修理费平均降低17%、设备综合效率提升4%。目前,齐大山铁矿、关宝山选矿、炼钢、彩涂、厚板、钒氮合金、鲅鱼圈、西昌钢钒等多个基地已通过建设智能工厂实现协同降碳。
其中,鞍钢矿业关宝山公司打造的国内首个选矿“黑灯工厂”成为近年来鞍钢集团推进协同降碳的经典案例。

鞍钢股份公司冷轧厂成品库 ▲
铁矿石是我国钢铁工业的保障性资源。由于国产铁矿存在“贫矿多、富矿少”的特点,加之随着矿产资源不断消耗,开采深度不断加大,矿山要想做强做优做大,必须从“脏、累、险”的中低端生产模式向绿色低碳、技术赋能、创新驱动的中高端生产模式转变。
鞍钢矿业公司是鞍钢集团重要的精品铁矿石生产基地,也是国内最大的铁矿石生产企业,承担着提高铁矿资源保障能力、维护钢铁产业链供应链安全的责任,是鞍钢集团“钢铁+矿业”双核战略中的重要一核。但经过常年高强度大规模开采,自2020年起,鞍钢矿业公司面临着产量下滑、刚性成本上升等诸多挑战。
“这些问题和挑战倒逼着企业必须去思考、去改变。”对于那时的困境,鞍钢矿业关宝山公司董事长兼总经理盖俊鹏也有切身感受。
以智能制造为核心技术的新一轮工业革命,为资源型产业发展变革带来了重大机遇。2021年以来,关宝山公司着手建设国内首个智能选矿“黑灯工厂”。仅时隔两年,鞍钢矿业关宝山公司的生产车间已是另一番景象。
走进关宝山公司的磨磁车间,无灯的生产现场空无一人,只有两台大型球磨机在快速运转,智能巡检机器人和清扫机器人闪烁着灯光在各处有序作业。
关宝山公司以智能化手段再造生产流程,由人工调控变为系统自主调节,借助选矿智能系统,促使磨矿、磁选、浮选等选矿流程工序协同、智慧生产、智能制造。
“过去,职工听球磨机的声音判断磨矿状态是否正常,现在,大数据技术把声音转化成数据,精准判断球磨机负荷;过去,职工看矿样判断品位,现在,品位分析仪通过光谱就能快速测量出矿石品位;过去,破碎工序每班次需要20多名职工,现在,通过智能布料系统、块度检测系统、胶带防护系统,50余台(套)设备全部实现远程一键操控……”关宝山公司职工说。
数字化智能化建设推动了关宝山公司效率效益的全方位提升,生产指标屡创佳绩,原矿处理量、精矿产量、金属回收率不断提高;设备效率稳步提升,球磨机效率、压滤机效率大幅改善;综合能耗持续下降,药剂单耗、电单耗、动力煤单耗逐步降低;劳动效率明显提高。
2022年,关宝山公司劳动生产率同比提高11.5%,年多产精矿1.1万吨。2023年上半年,关宝山公司生产量、销售量、成本、利润指标均超挑战值,利润超挑战值2610万元,铁精矿成本较2022年降低9.12%。
与此同时,关宝山公司通过建设ROC远程控制中心,实现了对直管机台的垂直管理,推动组织机构、岗位编制和业务流程同步优化:4个部门、5个区域,整合形成生产管控中心、运行保障中心和管理服务中心,破碎、磨磁、浮选、压滤等区域的生产操作权限全部集中到ROC远程控制中心,实现操作管理垂直化,提高管控效率,机构压缩66%、审批层级压缩43%、管理人员压缩至10人。盖俊鹏透露,关宝山公司正在与华为联合设计开发人工智能选矿系统。下一步,公司将继续精简人员,进一步提高公司产值和劳动生产率。
以鞍钢矿业关宝山公司为引领和协同示范,鞍钢矿业公司其他下属企业也在通过数字化智能化建设推进公司节能降耗,提高资源利用率和生产效能。今年前7个月,鞍钢矿业公司铁精矿产量再创历史最好水平,为建设高质量发展新鞍钢、辽宁实施全面振兴新突破三年行动提供了重要支撑。
矿业公司之外,在鞍钢集团推动多基地协同创新降碳的模式下,鞍钢股份炼钢总厂建成了世界上首个4.9GHz频段的5G工业专网,单转炉冶炼时间缩短4分钟,提高产能10%以上,成功投运全国首套钢水无人化运输系统,入选辽宁省首批5G全连接工厂。
鞍钢股份鲅鱼圈钢铁基地建成了沿海绿色智慧透明工厂,热轧废品率降低70%,厚板质量波动率降低20%,劳动生产效率提升1.5倍以上,成为钢铁行业智能制造建设新标杆。
鞍钢股份鲅鱼圈钢铁分公司完成了全流程超低排放改造,3大类72个超低排放改造项目已全部完成并实现全系统稳定运行,累计投入25亿元。
03
前沿技术,提升降碳能力
研发前沿技术,提升降碳能力,是鞍钢集团绿色低碳转型的“杀手锏”。
长期以来,我国钢铁行业以高炉—转炉长流程工艺为主。2021年我国长流程钢企吨钢二氧化碳排放量约为1.8吨(碳排放核算边界到钢坯工序),其中炼铁环节碳排放约占70%以上。针对这一问题,鞍钢集团组建团队加快研发低碳炼铁新技术。
2022年9月,鞍钢集团具有完全自主知识产权的全球首套绿氢零碳流化床高效炼铁新技术示范项目在鞍钢股份鲅鱼圈分公司开工建设,该项目致力于打造万吨级流化床氢气炼铁工程示范,实现了我国钢铁行业在低碳冶金新技术路线方面的重大突破。
谈起这项技术的研发过程,鞍钢经济研究院专家委员会办公室主任、研究员李成志说,氢冶金是钢铁行业实现低碳发展的重要路径,与传统碳冶金相比,氢冶金以氢气为燃料和还原剂,可以使炼铁过程摆脱对化石能源的依赖,从源头上解决碳排放问题。2021年7月,鞍钢集团与中国科学院、上海大学签订了绿色氢能冶金技术联合研发协议,经过一年多的前期技术攻关,万吨级流化床氢气炼铁工程示范项目开工建设,为世界氢冶金技术发展提供了“中国方案”。
在推进氢能冶金的同时,鞍钢集团还在废钢循环利用上发力。10月12日, 鞍钢集团钢铁研究院、鞍钢绿金产业发展有限公司与东北大学、辽宁陆帆集团、沈阳城市资源循环利用科技有限公司共同组建了主要针对废钢循环利用的“再生资源全生命周期循环利用联合创新中心”。
鞍钢集团钢铁研究院炼钢所所长兼鲅鱼圈分院院长廖相巍介绍,废钢的循环利用对于钢铁企业节能降碳作用明显。例如,生产1吨合格钢材,应用废钢相比于应用铁矿石要节省铁矿石1.65吨,并可降低350公斤标准煤的能源消耗,减少近三分之二的二氧化碳排放量和近80%的氮氧化物、二氧化硫等废气排放量,减少3吨左右固体废弃物的排放。
“鞍山钢铁将借助再生资源全生命周期循环利用联合创新中心,在报废汽车拆解、废钢循环利用、材料全生命周期管理体系研究等领域开展‘政产学研用’合作,推动再生资源回收与数字化赋能钢铁材料全生命周期等前沿技术开发与创新。”廖相巍表示。
据了解,作为东北地区最大的钢铁企业,鞍钢集团已将废钢产业作为“双核+第三极”战略格局的重要组成部分。鞍山钢铁以绿金公司为产业主体,坚持“绿色资源,绿色使用”发展路线,大力推动废钢产业发展,已在东北区域“邻钢而建”加工基地5个、“邻废而建”资源节点23个,产业规模达800万吨/年。同时,坚持产学研用同步推进,鞍钢集团钢铁研究院具备对废钢资源多年研发经验和多重技术储备。
此外,在研发新型炉料技术上,基于低碱高硅球团的低碳排放高炉炉料技术在鞍山钢铁带式机球团矿生产线实现产业化应用,获得 2022 年度世界钢铁协会“低碳生产卓越成就奖”。这项技术的突破为降低钢铁企业硫化物、碳氧化物、氮氧化物排放开辟了新路径。
2022年,鞍钢矿业公司“千米竖井硬岩掘进、地下高效充填”等先进技术助力国家“基石计划”项目全国最大的单体地下铁矿山西鞍山铁矿开工建设。建成投产后,该矿山将成为一座年产铁精矿千万吨级、技术领先、绿色、智能、无废、无扰动的世界一流地下铁矿山。
李成志介绍,2022年,鞍钢集团研发经费投入强度提升到3.88%,研发经费投入达130.56亿元。下一步,鞍钢集团将继续加大科技研发投入力度。
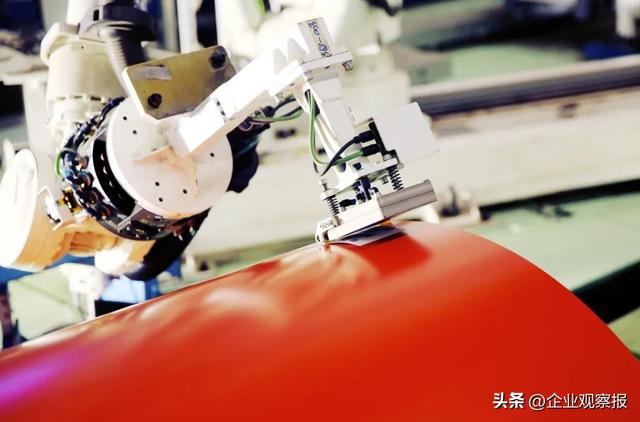
鞍钢股份冷轧厂彩涂分厂机器人正在给彩涂卷贴标签并完成产品身份录入 ▲
04
复垦改造,打造绿色矿山
“绿色矿山”,是鞍钢集团绿色低碳发展的重要路径之一。
2023年全国“两会”期间,外交部部长助理、发言人华春莹在社交媒体上连发5组卫星对比图,展现过去10年中国的变化,鞍钢集团矿山生态保护典型成果——鞍钢矿业大孤山铁矿东山包尾矿库就在其中。
“国家级绿色矿山”——鞍钢矿业大孤山铁矿废弃的排岩场经过多年复垦绿化,已被打造成了林深树茂、花果飘香的鞍钢矿业生态园。整个矿区春季有花、夏季有荫、秋季有果、冬季有景,厂区植被覆盖率达到了98%以上。
以大孤山铁矿为代表的鞍钢矿山的生态修复,早在本世纪初就开始了。“第一批进行绿化复垦的职工早已退休,一代代鞍钢人接力传承,把绿化复垦这项工作持续了下来。”聂振勇说。
修复矿山,并非易事。鞍钢矿业战略发展部有关负责人说,大孤山排岩场的修复治理至今已有20多年,矿山排岩场土壤来自尾矿,水来自矿坑,技术人员因地制宜,最大限度降低成本,高效率改造,进行了多轮土壤技术研发以提升土壤质量。
昔日尘土飞扬的排岩场、尾矿库,如今变成了风光秀丽的多功能生态园,大孤山铁矿排岩场边坡复垦模式为后来其他矿山边坡的复垦提供了重要实践经验。
近年来,鞍钢集团在严格遵循矿山相关治理标准的基础上,号召矿业公司、攀钢等下属单位持续加强矿区环境治理,打造生态矿山。其中,矿业公司超额实施《2020—2022 年矿山生态修复规划》,2020—2022 年企业自行治理487.80公顷,其中2022年治理243.53公顷,矿山可复垦率近100%;攀钢按照边开采、边治理原则,滚动修编生态恢复规划,制订年度实施计划,积极推动矿山渣场生态恢复治理,2022年完成马家田尾矿库、巴关河渣场等生态恢复共191公顷。

鞍钢矿业公司生态园 ▲
截至2022年,鞍钢集团完成矿山生态修复3800余公顷,复垦率达到91.6%,16座矿山企业被评为国家级“绿色矿山”,大孤山休闲旅游园、眼前山绿色采摘园、前峪尾矿库苗木培育园三个生态园区被授予“国家绿色矿山示范基地”和“中小学研学基地”称号。
鞍钢集团还充分利用矿山排岩场、尾矿库等土地空间资源推动光伏发电项目。目前,鞍钢集团现有光伏、风电项目(含在建)装机容量约200MW,在建鲅鱼圈焦炉煤气制LNG(液化天然气)联产氢气项目,项目建成投产后预计年产LNG12.5万吨、氢气2400万立方米,每年减排二氧化碳50万吨、二氧化硫170吨、氮氧化物1300吨。
近期,工业和信息化部、国家发展改革委、财政部等七部门联合印发的《钢铁行业稳增长工作方案》提出,2023—2024年,钢铁行业稳增长的主要目标是:2023年,钢铁行业研发投入力争达到1.5%,工业增加值增长3.5%左右;2024年,钢铁行业高端化、智能化、绿色化水平不断提升,工业增加值增长4%以上。其中强调,加快推进钢铁企业超低排放改造工程,探索打造超级能效工厂,加大对氢冶金、低碳冶金等低碳共性技术的支持力度。
对于国内钢铁行业及鞍钢集团的下一步发展方向,鞍钢集团董事长、党委书记谭成旭指出,未来10年是中国钢铁产业发展由“大”到“强”的关键期。钢铁行业需要强化以绿色低碳需求为创新导向,加大创新资源投入,重点围绕氢冶金、低碳冶金、薄带铸轧、极致能效、绿色环保等领域关键共性技术,形成一批前瞻性、突破性、颠覆性技术,打造世界钢铁绿色低碳原创技术策源地。
据了解,鞍钢集团将坚定不移地把绿色低碳转型作为驱动高质量发展的重要引擎,积极参与全球低碳冶金创新联盟等平台,按照鞍钢集团低碳冶金路线图,加快研发应用低碳冶金技术,进一步推动能源低碳转型,提高能源利用效率和清洁生产水平,打造绿色低碳发展典范和世界一流的影响力。