曼恩斯特固态电池级片制造解决方案,破局固态电池量产难题
(转自:曼恩斯特)
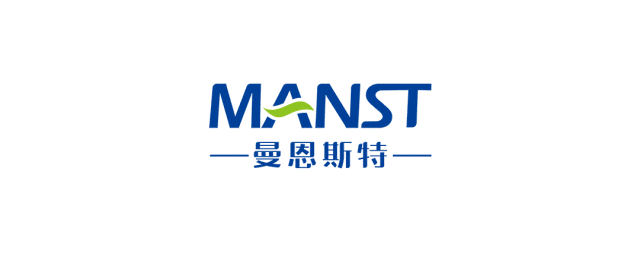
当全球电池企业竞相攻克固态电池技术时,量产之路始终卡在制造环节。传统湿法工艺面对固态电解质时暴露出明显短板:硫化物电解质遇溶剂分解的毒性风险、固-固界面阻抗失控、烘干工序能耗居高不下,据测算,仅电极涂布和干燥环节就占锂电池生产总能耗的30%以上。
面对这些行业共性难题,曼恩斯特从制造端重构生产逻辑,将干法工艺作为核心突破口,推出固态电池级片制造解决方案:从制膜,到电极制备,再到固态电池前段产线,不仅自研关键设备,还构建起一整套以干法工艺为主的前段产线。
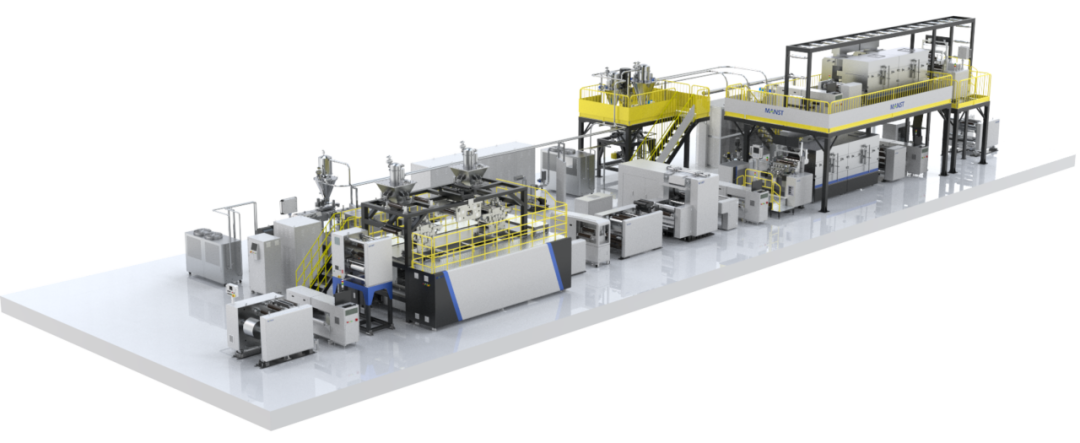
其中,全陶瓷双螺杆纤维化、14辊双面压延、湿法电解质薄涂三大核心自研设备,构建起了该固态电池极片制造方案的技术护城河,助力固态电池走向大规模量产。
01
全陶瓷双螺杆纤维化技术
曼恩斯特干法工艺的核心设备创新始于纤维化环节。曼恩斯特自研的全陶瓷干法双螺杆纤维化机,采用陶瓷机筒内衬与螺纹元件,从根源杜绝金属异物引入,保障电芯安全性和长循环寿命。陶瓷材质赋予设备卓越的耐磨性,使用寿命≥18,000小时;同时其模块化积木设计便于拆卸清洗,灵活适配小试、中试到量产不同阶段需求。
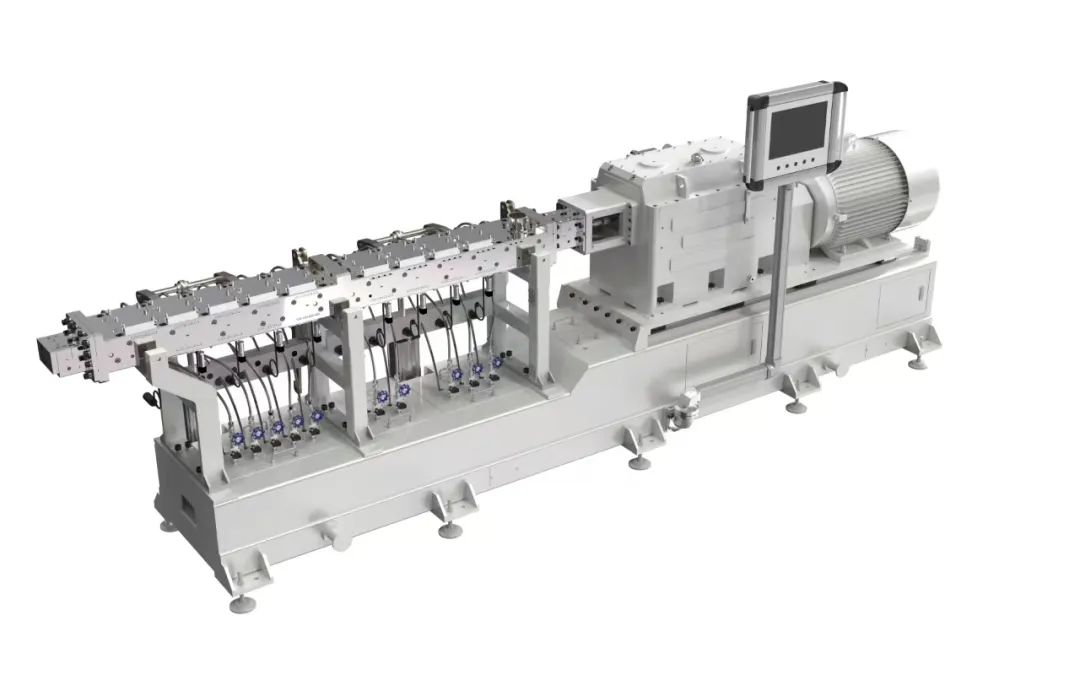
在PTFE粘结剂的19℃相变温度窗口,设备精准施加剪切力,将PTFE晶体撕裂为纳米级纤维网络,高效实现原料的纤维化,形成稳定均匀的电极骨架。双端支撑结构有效减少轴挠度变形,中试线处理量达150L/h。这一技术突破不仅解决金属污染导致的电池微短路风险,更为后续均匀成膜奠定基础。
02
14辊双面同时成膜工艺
均匀性控制是干法工艺应用的另一难关。为了保证极片原料成膜品质,曼恩斯特引入14辊双面同时成膜工艺,实现双面同时均匀成膜。配套的钢带预成膜机构采用斜模压缩设计,可以对多辊压延设备提供持续、定量、稳定的喂料,将显著提高膜片的压实密度以及膜厚、密度均一性。
实测表明,该成膜工艺将膜厚波动压缩至±3μm,这一精度水平远超传统单面成膜工艺,为高一致性极片量产提供可能。
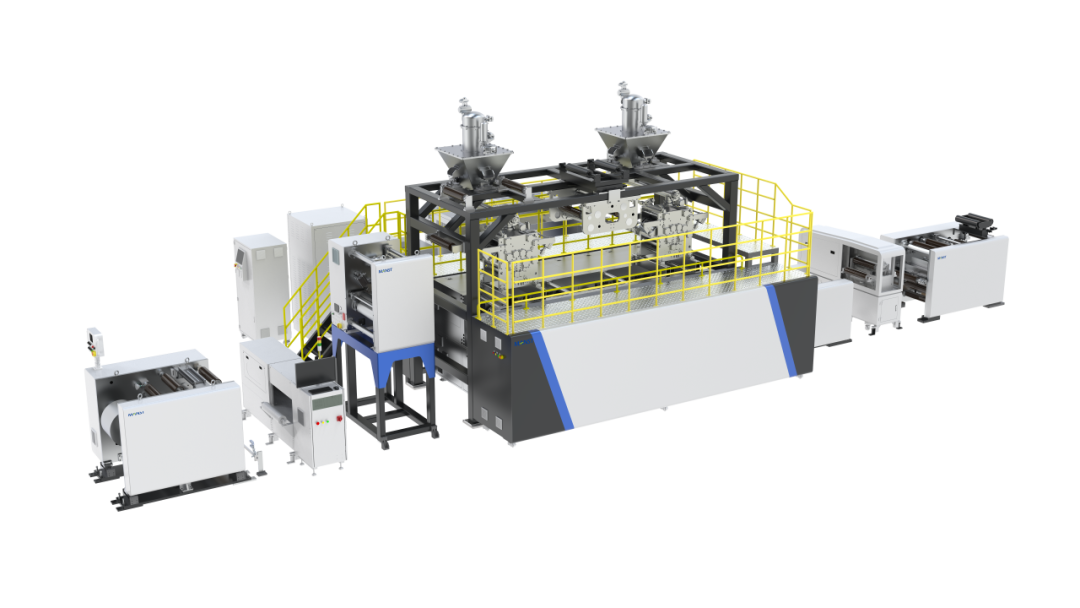
对于成膜压延设备,小试线中试线可以选用单面成膜复合设备,中试线和量产线可以选用双面成膜复合设备。双面成膜复合一体机一体化设计使得复合过程更加紧凑、高效,提高了生产效率,精确的张力测量和调节机构确保了复合过程中的张力稳定,避免了膜片变形或起皱的问题,自动收卷机构能够准确地将复合好的膜片卷成合适大小的极片膜卷,降低了操作难度和人工误差。
03
湿法电解质薄涂系统
固态电解质在涂布前需经过砂磨机处理,使电解质粉体更细腻,进一步提升电芯的整体性能。在极片上薄涂固态电解质层时,曼恩斯特采用湿法狭缝涂布技术与砂磨机处理工艺,实现非接触式薄层涂布,并采用“正面涂覆→烘烤→反面涂覆→烘烤”的双面涂布工艺,有效避免界面混溶问题,确保固态电解质层的均匀性和稳定性。
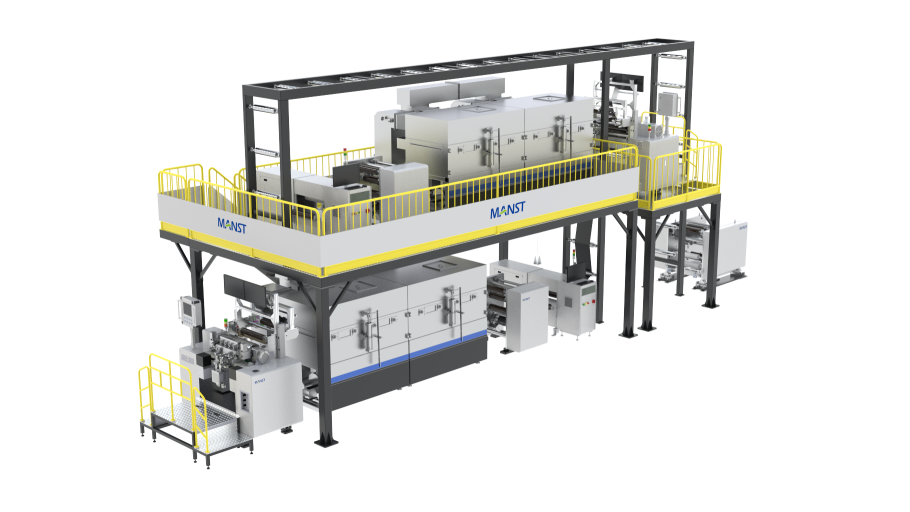
值得一提的是,固态电池设备的集成化是曼恩斯特明确的发展方向。通过将加料、混料、纤维化、制膜、辊压、分切和收卷等环节整合在一组设备中,不仅可以减少物料在各工序间的流转时间,还可以有效提升生产效率和产品一致性。
通过自研关键设备构筑技术闭环,曼恩斯特为行业提供了以干法工艺为主的前段产线选择,验证了一条可落地、可量产的路径。
未来,曼恩斯特将持续深化干法工艺与设备集成的协同创新,突破固态电池制造的成本与技术瓶颈,携手产业链伙伴迈入更安全、更高性能的固态电池量产进程。
As global battery enterprises race to conquer solid-state battery technology, mass production remains bottlenecked at the manufacturing stage. Traditional wet processes reveal significant shortcomings when handling solid electrolytes: toxic risks from sulfide electrolyte decomposition in solvents, uncontrollable solid-solid interfacial impedance, and persistently high energy consumption in drying processes. Estimates indicate that electrode coating and drying alone account for over 30% of total lithium battery production energy consumption.
Confronting these industry-wide challenges, MANST has reengineered production logic from the manufacturing end, establishing dry processing as the core breakthrough. The company has launched a solid-state battery electrode manufacturing solution encompassing film formation, electrode preparation, and complete front-end production lines—not only self-developing key equipment but also building an integrated front-end production system centered on dry processes.
Three core self-developed technologies form the solution's technical moat:
1. Fully Ceramic Twin-Screw Fiberization
2. 14-Roll Double-Sided Calendering
3. Wet Thin-Coating of Solid Electrolyte
These innovations accelerate solid-state batteries toward mass production.
MANST's dry process innovation begins at fiberization. The self-developed Fully Ceramic Dry Twin-Screw Fiberization Machine employs ceramic barrel linings and screw elements, eliminating metallic contamination at the source to ensure cell safety and long cycle life. The ceramic construction delivers exceptional wear resistance, with a service life ≥18,000 hours. Its modular "building block" design facilitates disassembly and cleaning while flexibly adapting to pilot-scale, pilot-line, and mass production requirements.
Operating within PTFE binder's 19°C phase transition window, the machine precisely applies shear forces to tear PTFE crystals into a nanoscale fiber network. This efficiently achieves material fiberization, forming a stable, uniform electrode skeleton. Dual-end support minimizes shaft deflection, with pilot-line throughput reaching 150 L/h. This breakthrough not only solves micro-short circuit risks from metal contamination but also lays the foundation for uniform film formation.
Uniformity control presents another critical hurdle. To ensure film quality, MANST introduced 14-roll double-sided simultaneous film formation. The matching steel belt pre-forming mechanism uses an oblique wedge compression design to provide continuous, quantitative, and stable feeding for multi-roll calendering. This significantly enhances film compacted density, thickness uniformity, and density consistency. Testing confirms this process compresses thickness variation to ±3 μm—far surpassing traditional single-sided methods—enabling high-consistency electrode mass production.
Note on equipment selection:
Pilot/pilot-line: Single-sided film formation composite equipment
Pilot-line/mass production: Double-sided film formation composite equipment
The integrated double-sided film formation composite unit features a compact design for higher efficiency. Precise tension measurement and adjustment mechanisms ensure stable tension during lamination, preventing film deformation or wrinkling. Automatic winding accurately rolls laminated films into appropriately sized electrode rolls, reducing operational complexity and human error.
Solid electrolyte coating requires pre-treatment in a sand mill to refine powder particles and enhance overall cell performance. For thin-layer coating of solid electrolyte onto electrodes, MANST employs wet slot-die coating technology combined with sand milling. This enables non-contact thin-layer coating using a dual-side process: "front coating → baking → back coating → baking." This effectively prevents interfacial miscibility issues, ensuring electrolyte layer uniformity and stability.
Crucially, equipment integration is a defined strategic direction for MANST. Consolidating feeding, mixing, fiberization, film formation, calendering, slitting, and winding into a single equipment set reduces material transfer time between processes while significantly boosting production efficiency and product consistency.
By establishing a closed-loop technology ecosystem through self-developed key equipment, MANST provides the industry with a dry-process-dominated front-end production line option, validating a viable path to mass production.
Moving forward, MANST will deepen synergistic innovation between dry processes and equipment integration, breaking through solid-state battery manufacturing's cost and technical barriers. The company will collaborate with industry partners to advance the mass production of safer, higher-performance solid-state batteries.
文案丨十二
美编丨十二
审核丨魏小姐