北方导航公司自主研发成功兵工行业首条智能化柔性检测线
转自:中工网
工人日报-中工网记者 赖志凯 通讯员 李丰华 张巍
“MES已建立连接,PLC已建立连接,线激光已建立连接,影像仪已建立连接,三坐标已建立连接……”“工控机已发送数据。”“数据库成功收到数据!”“我们已严格按照工艺要求完成零件的自动化检测!”
这是北方导航控制技术股份有限公司智能控制技术团队成员连续作战的第128天。他们锚定目标、紧盯节点,各司其职、齐心协力,夜以继日扎根在车间生产一线,在产线上不断尝试、创新突破,最终,自主研发建成兵工行业内首条智能化柔性检测线。该检测线以分布式控制架构、多技术融合体系和显著效能提升,成为兵工领域智能制造的标杆样本,已申报专利3项,软件著作权1项。
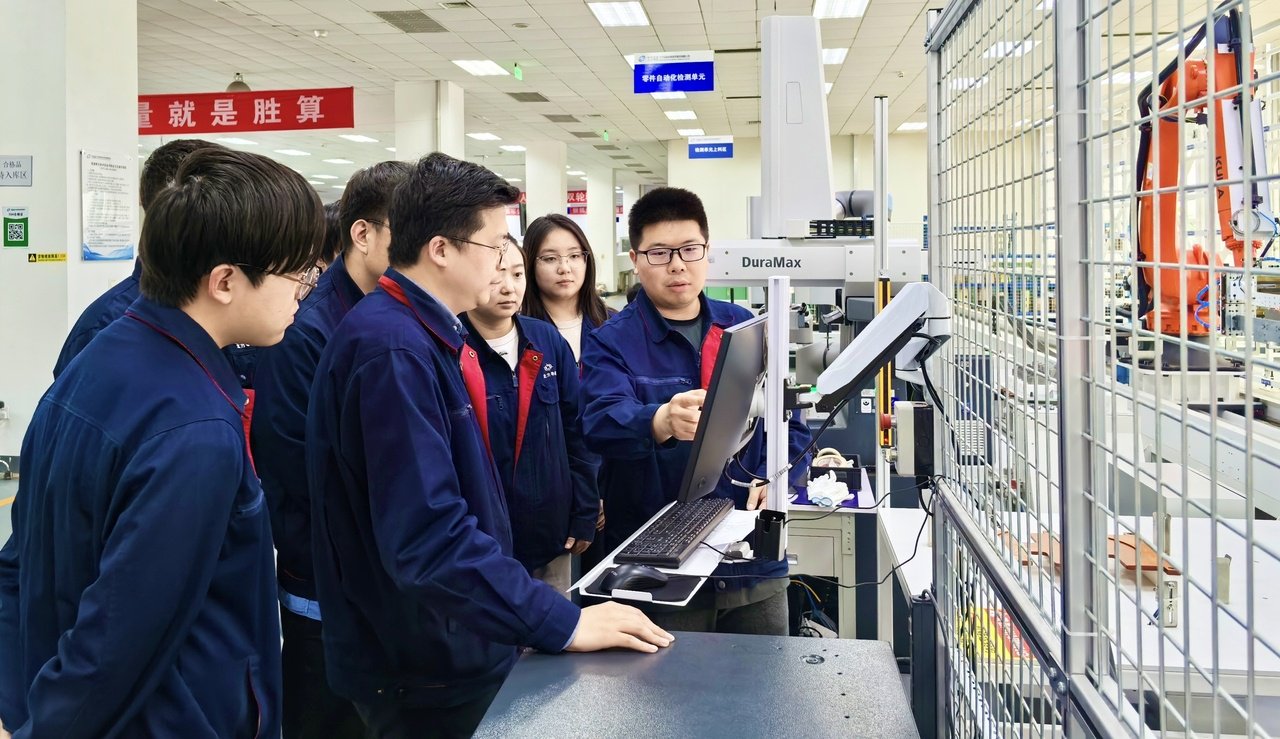
从“三大痛点”到柔性检测新范本
“大家发现目前工人们检测零件的过程存在哪些问题吗?”一次项目组例会上,智能控制技术团队负责人王武抛出了一个引人深思的问题。
“人工成本太高,需要一人手测一人记录,频繁更换量具不说,效率还很低,一旦某个岗位缺人,整个流程都得停。”小李率先回应。
“设备响应也太慢了,灵活性不足,新型号一来,我们就得重新写程序。”小贡补充说。
“还有数据散乱,检测完的结果没人管,查问题要翻纸质记录,时常存在错记漏记的情况。”小黄紧锁眉头说道。
随着一场深层次的交流在小组内展开,最终项目组归纳总结出当前检测线面临的“三大痛点”:人工成本高、响应速度慢、数据管理弱。
作为项目负责人的王武提出:团队将自主设计建设一条智能化柔性检测线,通过采用分散控制和集中管理的设计思想,把复杂系统的多目标求解问题逐层划分为复杂程度相对较低的子问题,提升产线的灵活性、鲁棒性和抗干扰能力,从而实现多个智能机器协同工作的场景,最终将传统军工检测所面临的“三大痛点”逐一攻克,并完成“三大核心目标”:实现降本增效、提升产线灵活性、打通数据流通瓶颈。
有了清晰的目标和思路后,大家集思广益、群策群力,常常围绕技术细节展开激烈的讨论。
“这批新增的零件型号和之前的不一样,是否需要重新编七轴机器人搬运程序?”项目组成员小李皱着眉头问。
项目组成员小贡笑着说:“不用了,我们设计了托盘标准化,搬运程序跟零件无关,系统会自动识别和分发检测任务,新零件‘即插即用’。”
小李听完眼睛一亮,问道:“那如果检测设备不够用了,需要增加呢?”
另一成员小黄则回应道:“没有问题,我软件上添加一个线程专门与新增的设备交互即可,不影响整条产线的使用。”……
针对传统集中控制模式“牵一发而动全身”的弊端,项目团队创新性构建了“1+N=1”分布式协同制造控制系统。每一台检测设备都拥有自主通讯与控制逻辑,通过上层调度系统集中协调运行任务,构成稳定、高效、可动态扩展的检测网络。
此外,该产线还配置了复合检测单元,同时支持在线模式和离线模式检测,离线模式时只需手动放置托盘即可自动检测并上传检测结果,进一步增强了产线灵活性。系统同时引入人工预检环节,确保检测闭环、数据完整,打通了产品质量追溯的“最后一公里”。
最终,在这一先进架构的助力下,新建成的智能化柔性检测线攻克了传统军工检测线的“三大痛点”、完成了“三大核心目标”,实现了真正意义上的“产品可变、工艺可调、产线稳定”,为现代军工产品的柔性制造和快节奏迭代提供了强有力的支撑。
构建全要素智能检测生态
该智能化柔性检测线集成三坐标测量仪、影像仪、线激光扫描仪等尖端设备,覆盖板类、轴类、舱体类零件的几何尺寸、形位公差等全维度检测需求。搭配EROWA零点定位系统与柔性工装夹具,实现设备间高精度互换、快速装夹,检测通用性与精度双提升。
在物流与执行层面,KUKA七轴机器人与UR协作机器人承担主线搬运与设备之间的物流任务,协作机械臂结合自动换抓手装置,实现对不同零件的自适应搬运与快速部署,提升了系统整体运行效率。
在软件方面,MES系统作为产线“大脑”,全面接管从任务生成、计划排产到库存管理、检测反馈、质量分析的全流程数字化管控。
新产线投用不久,车间里已悄然弥漫着变化的气息。
检测线前,老工人刘师傅站在数据看板前,看着自动检测数据滚动更新,忍不住感慨:“以前一批零件得靠人工慢慢测好几天,现在两台机器人一配合,实现自动化检测,十几个小时就搞定了,还不用我们操心对错。”
旁边的小张也接话道:“是啊,而且还把我们从繁琐的工作里解放出来了,咱们现在主要是盯着系统报警,做些关键节点预检,轻松多了!”“这就是智能制造啊!”刘师傅笑着说,“以后干活靠的是脑子,不光是手了。”
控制软件基于LabVIEW开发,采用多线程架构与生产者-消费者模型,支持多个检测设备、工位、控制节点间的实时通信与同步控制。具备设备掉线重连、异常状态自复位、任务接续处理等关键功能,确保系统高鲁棒性、高可用率。数据以标准化JSON格式传输,便于上位系统存储与分析,为企业后续数据挖掘与智能决策提供基础支撑。
“传统工艺”向“数字智控”跨越
智能化柔性检测线全面投用后,成效显著:检测效率提升10倍,人员由10人压缩至2人,年节约人工成本超150万元;同时,系统检测误差稳定,结果一致性强,极大提升了产品出厂一致性与可追溯能力。
目前,此检测线作为智能制造标杆项目,吸引了多家单位前来调研交流,在行业内形成了积极示范效应,具有极高的可借鉴及推广价值。这也标志着我国军工制造从“传统工艺”向“数字智控”的跨越式升级。
在一次内部总结会上,王武非常有感触地说:“这条检测线不仅是技术的突破,更是理念的转变。未来的制造,拼的不仅是速度和质量,还有柔性、智能和响应力。新质生产力,不只是口号,它就在我们脚下的每一条产线上生根发芽。”
据介绍,智能控制技术团队在成立的短短7年时间里,取得20余项技术创新、10余项关键突破,累计为企业节约成本超5000万元,形成11项专利/软著、2项行业标准,斩获中国质量技术奖、工信部智能制造优秀场景、兵器集团科技进步奖、兵器集团工艺技能协同创新奖、兵器集团装备质量建设突出贡献团队等多项荣誉。