中国一重:以“数”为翼 乘“数”而上
转自:黑龙江新闻网
干净整洁的车间内,一台无人值守的柔性生产线正在自动加工,其工序交接由一台6轴关节机器人自动完成,机械手从上料台将产品运送托抓取到立式加工中心,自动装卡后进行零件精加工。这里正是一重集团(黑龙江)专项装备科技有限公司(以下简称为一重专项)的专项产品数字化制造车间。
老工业基地转型,老牌央企重焕新生,走在转型前沿的中国一重很早就将目光聚焦数字化转型。
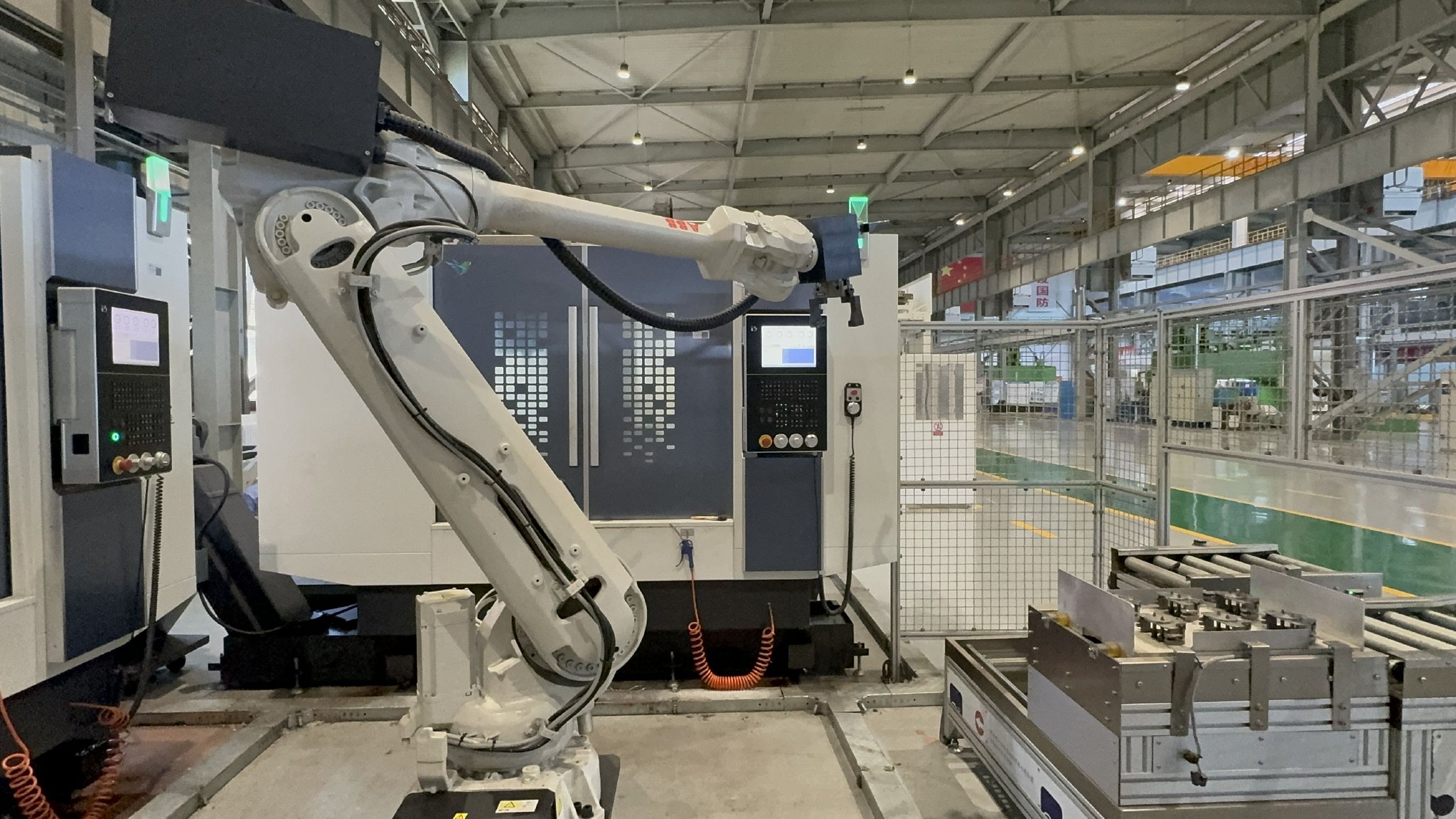
实现关键业务数据100%进入系统,提升产品异地网络化协同能力,研发周期缩短40%,车间资源效率配置提升50%,关键工序质量可追溯质量100%……这是数字化转型为一重专项带来的变化。而这变化背后要从专项产品数字化制造车间的建设说起。
一重专项制造中心副总经理毛哲说,专项产品数字化制造车间的初衷就是扩大产能,车间在设计之初就考虑了数字化所需要的硬件。
以排屑为例,毛哲说:“机械加工过程中会产生很多铁屑,传统的车间里会有排屑器将铁屑集中收集起来,再由车辆统一运走。而我们的车间在地下设计了排屑通道,机床加工完零部件,将自动排屑系统打开,铁屑就被自动收集走,在车间里完全看不到铁屑,实现了全厂房的集中排屑。”
“不仅如此,建设过程中,我们还将监控、网络设备等内嵌到厂房内,并留有接口,未来可不断进行数字化升级改造。”毛哲说。
数字化过程中,硬件与软件缺一不可,需要二者的有机结合。

毛哲说:“在软件方面,我们有成熟的产品生命周期管理平台(PLM)和制造企业生产过程执行系统(MES),前者可以实现从生产零件的毛坯开始,到加工、装配、出厂全生命周期的管理,后者可以针对车间的工作量进行分配。同时,我们对基于MES系统的质量管理系统和供应链管理系统也进行了信息化的互通。”
基于这些系统就可以实现研发、设计、管理、制造等信息的实时交互,提高了工作效率。这一变化在生产中是十分明显的。专项产品数字化制造车间内实现了机床全部联网,这意味着什么?毛哲说,当前机床的转速、净给量都是有记录的,正在执行的什么工艺、哪个程序都可以一目了然,也方便统计工作量。
同样进行了软件和硬件全面优化升级的还有中国一重铸锻钢事业部炼钢厂内的大型铸锻件洁净钢平台。通过一张大屏,可以清晰地看到各项生产数据以及炼钢厂内主要炉台的实时生产画面。
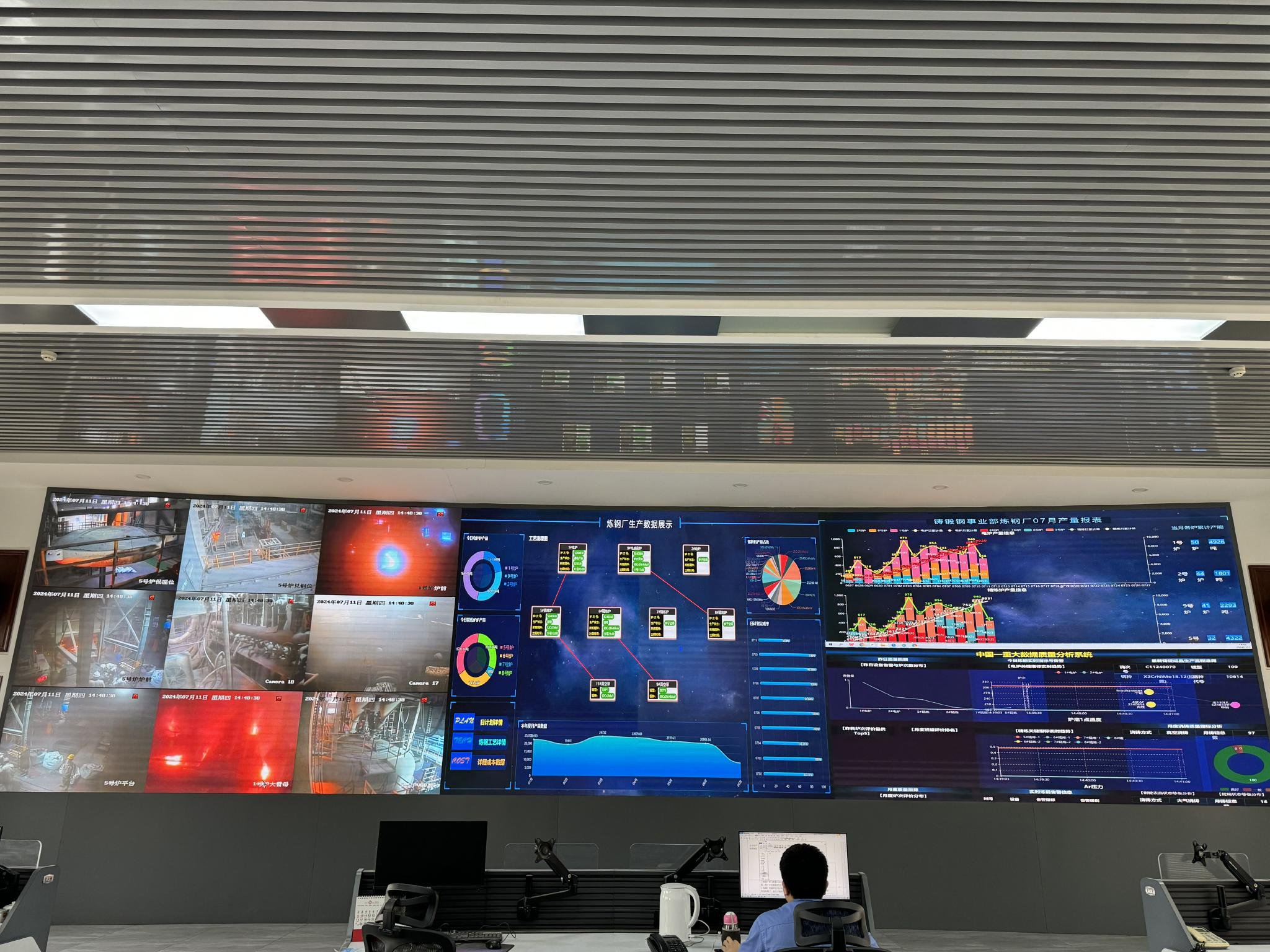
炼钢厂设备科点检员张瑜说:“我们把原来的炼钢数据进行信息化整合,由纸质报表整合到MES系统,工艺数据管理和查询更加便方便,检化验试样从检测到结果传输更加便捷,使各工序间协作配合更加透明,缩短了各环节的生产周期,优化了生产工艺,提高了生产效率。”
在中国一重龙申(齐齐哈尔)复合材料有限公司(以下简称一重龙申)的生产车间内,S11叶片的模具正在安装。“模具安装完进入到生产阶段时,我们会同步对5G数字化项目进行试运行,全流程参与到叶片的生产环节,通过这种实际应用来检测是否需要进行系统的改进优化。”一重龙申技术部副部长李永江说。
李永江所说的5G数字化项目,是一重龙申在2023年上马的新项目,可以将传统的业务模块整合到企业资源管理平台(ERP)中,从订单签收到计划生成再到执行、工艺流程等都在系统中生成,可通过电子大屏查看生产中每个项目的具体情况。

推进数字化转型升级,是中国一重推动新质生产力发展的关键路径。铸锻钢事业部炼钢厂获评2023年黑龙江省数字化(智能)示范车间。前不久,一重专项的专项产品数字化制造车间获评为2024年黑龙江省数字化(智能)示范车间。
其实,不仅是炼钢厂和一重专项,行走在中国一重的各个厂区,这里的大型设备已大多接入5G专网,研发、设计、管理、制造信息实时精准交互,运行分析和辅助决策的系统性、精准性、及时性、科学性不断提升,关键设备、软件国产化替代率不断提升……
一张数字工厂的蓝图已经清晰绘就:3年内,中国一重的研发设计要实现跨地域、跨专业的并行协同,生产单位将全部建成数字化车间和智能生产单元,车间生产效率将再提升15%以上。
记者 孙铭阳