科林电气:设备上“云”,为企业发展按下“快进键”
转自:河工新闻网
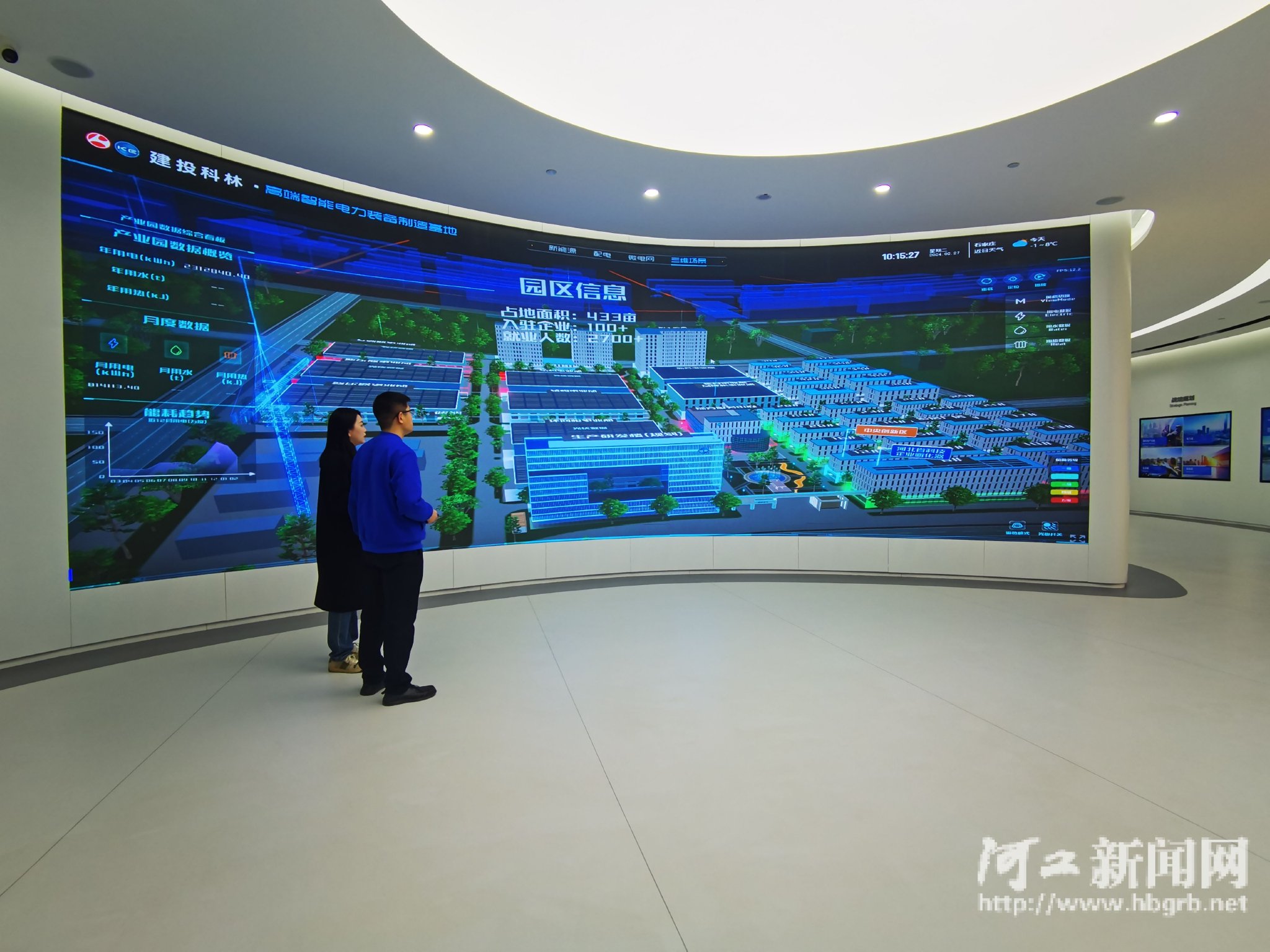

智能柔性生产线上“云”后,员工只需设置参数,产线就能自动完成全流程工作。
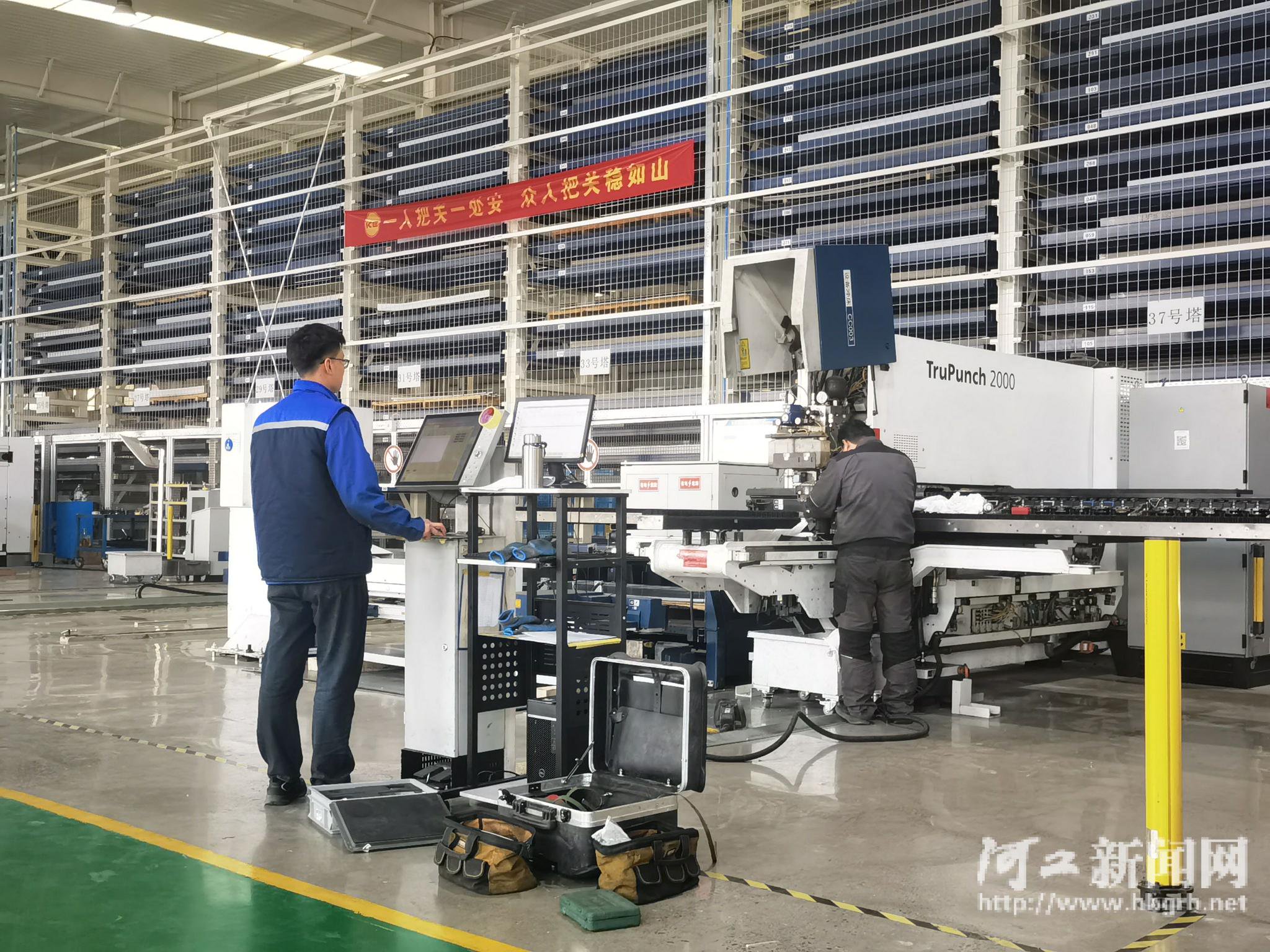
智能柔性生产线上“云”后,员工只需设置参数,产线就能自动完成全流程工作。
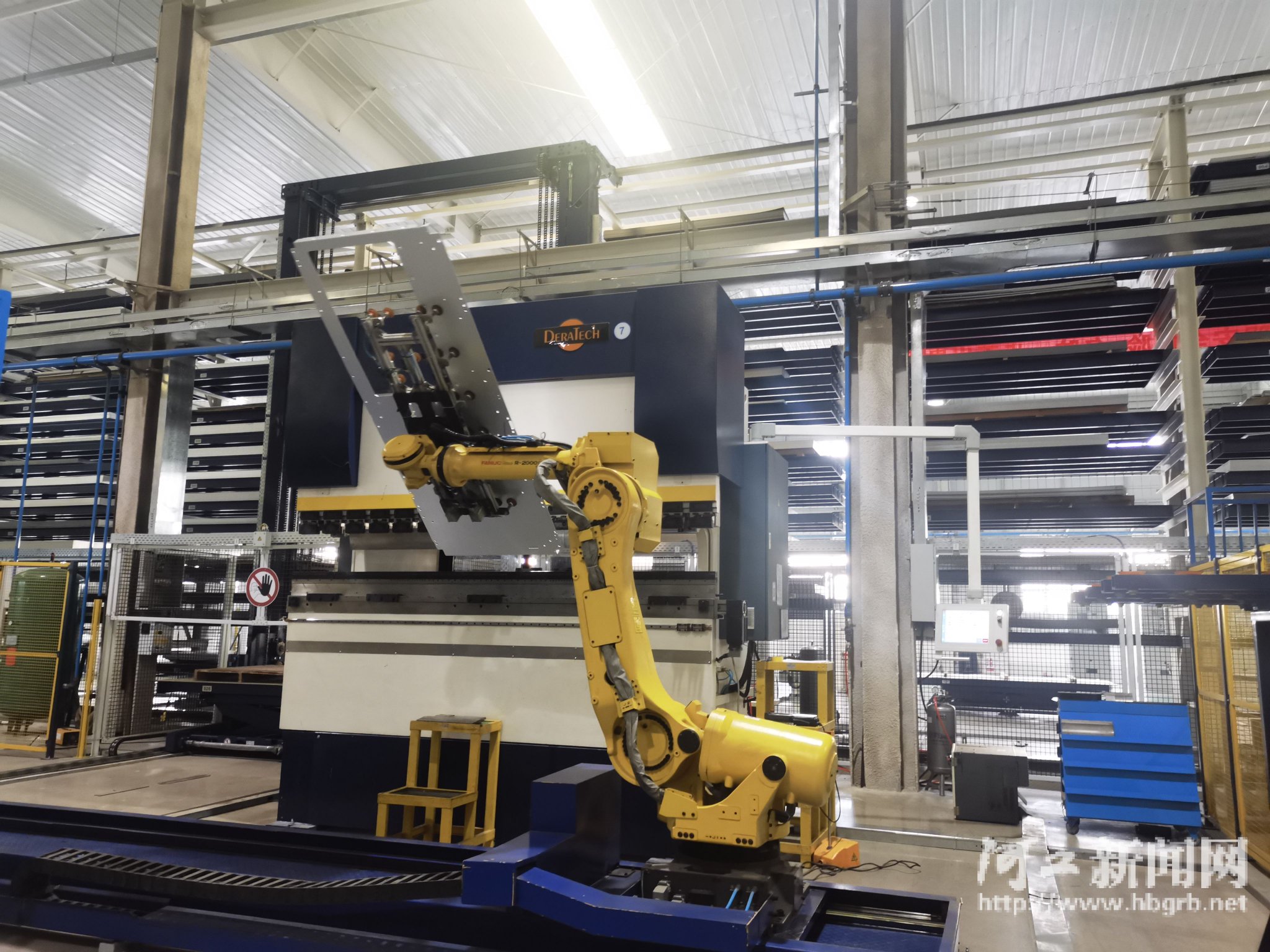
2月27日,石家庄科林电气股份有限公司(以下简称科林电气)结构事业部智能柔性加工中心,自动化折弯单元正在作业,伴随着机械臂的腾挪翻转,一片大重量的金属板材被放置在机床上,抓取、定位、折弯、码垛……这是科林电气去年投产的智能柔性生产线,正为公司的智能配电柜设备生产开足马力。
而在科林电气云数据中心一块巨大的液晶显示屏上面,不同颜色的电能负荷标识,也将结构事业部等相关部室的用电情况、运行状态清晰地展示出来。
将新一代移动通信、工业互联网、大数据分析等先进数字技术应用在传统电气装备行业中,深入推进制造业与互联网融合发展,科林电气由一个传统的硬件设备提供商转变成智慧能源建设引领者,不仅为用户提供了智慧能源建设整体解决方案,也加速推进了企业自身向数字化、网络化、智能化转型的步伐。
设备“上云”,打造“智慧工厂”
科林电气智能柔性加工中心,引进了全球领先的数字化智能钣金生产线,通过人、机器、自动化装置与数字化软件的智能协作,实现了全数字化,全天候全自动化智能生产,是一座名副其实的“智慧工厂”。
这座“智慧工厂”由钣金加工柔性生产线、全自动化折弯机、自动化激光冲床复合机、全自动化数控冲床等部分构成,生产工序以智能料库为中心,呈椭圆形排布。“只需将板材零件信息录入系统,产线就可自动调取智能料库中的板材,完成冲切、折弯,无需人工干预。”科林电气智能柔性加工中心产品设计技术人员李帅介绍。
在数控加工工序,一名员工正在为全自动高速数控冲床设置参数,他告诉记者,以前,一台冲床就需要3个人,工作时,他和两位同事,一起搬起平均重量150公斤的板材,先切割,接着分拣零部件,工作强度大、效率低。
引进智能柔性生产线并连上云系统后,员工只需设置参数,产线就能自动完成全流程工作。如今,两个人就能操作整个车间的4台冲床,一个班就能减少10人,而生产效率陡增。
沿着生产线走到折弯工序时,记者看到3个机械臂正在按程序作业。从抓取半成品到放入机器折弯再到取出码垛,机械臂一气呵成。
“这是由三台自动化折弯机组成的自动化折弯单元,可以实现全自动化智能离线编程,智能化料库系统更是改变了材料原始的存放模式。”李帅说,过去3个工人抬着半成品折弯,现在1个机械臂就能自动完成。生产效率提升了5至8倍,折弯精度达到0.01毫米,产品质量稳定性也得到大幅提升。
同步上云的生产数据不仅完成了数据库的积累,有了完善的追溯体系,还可以根据实际需求,对生产线进行快速的切换和调整,灵活调度生产资源和设备,“如果我们有加急订单,云数据平台可以进行排产,调整生产线的产能和节拍。”李帅说,个性化的数据加上全自动智能化生产,公司的订单可以趋向于定制化,有效降低备货成本和库存成本,实现“定制化生产、即时交付”。
设备上“云”,显著提升了设备运行效率和综合管控能力,更为企业发展按下了“快进键”。
智慧互联,全面掌控能源使用
“这是我们开发的人工智能综合能源管控服务平台,这个平台只需要一个人的操作,就能查出整个园区、电网、充电桩等数据,这是我们智慧能源的新大脑。”科林电气研究室主任袁玉宝介绍,公司借力互联网,从单纯卖设备向提供智慧电力系统整体服务的转变,也是基于客户需求做出的产品链延伸。
这个平台,最佳应用代言就是科林产业园智能化大数据监测系统。
科林产业园聚集了人工智能、电子信息、智能电网、高端装备智造、新能源五大战略新兴产业近100家企业入驻。通过这个监测系统,一个人就能监测600多亩园区的上百家企业的水、电、热数据,还可对能源进行统一调度、降低企业综合能耗和提高劳动生产率,帮助客户更有效地使用能源。
以科林电气为例,为保障生产所需电力能源,科林电气在屋顶安装了10兆瓦分布式光伏电站。没有接入大数据平台前,需要进行人工实地巡检,两名员工实地巡检一圈,至少用时两天。接入大数据平台后,员工每周只需实地例行巡检一次,平时都是平台自动巡检。平台自动识别故障发出提醒后,运维人员再及时解决。
在平台上,每台设备都有对应的运行曲线。“比如,最近清理完毕光伏板上的积雪,我们再通过前后数据对比,判断发电量是否恢复。”如果某个设备数据偏低,他们就会提前干预,排除隐患。
大数据平台对企业生产的监测更为直观,工作人员点击“铸造设备”检查设备运行状态时,屏幕上立即显示出当日设备运行曲线。设备空闲或超负荷,通过平台一目了然,便于生产调度。
同时,车间机器出了故障,利用智能化大数据监测系统,只需点几次鼠标,两三分钟就能从园区成千上万的供电线路里找到问题点。
“这要搁在以前,因为设备异常运行无法预警,且不说不能及时发现问题,就是发现了问题,查找原因也得耗费很长时间,那时损失已经造成了。”袁玉宝说。
数据赋能,车间越来越“聪明”
在数字化这条赛道上,对于企业来说,打破信息孤岛,实现各环节数据互联互通,提高协同效率,最终实现智能生产和精益管理,一直是急需解决的首要问题。
科林电气正在研发的“生产交付系统平台”,就是奔着这个难题而去的。
“这个交付系统是针对生产履约开发的一款协同软件,目的是将现有的两个系统连通,打破信息孤岛,在这个平台上建立一种高效的协同,以便我们更好地通过大数据和信息化手段,对功能性模块和自动化设备进行优化管理,实现生产过程的可视化和数据化,提高企业的生产能力和交付效率。”科林电气生产中心主任李计朝介绍。
在规划中,这个平台将覆盖生产、计划、质检、供应链等所有核心环节,通过数据协同,打破生产管理和供应链协作中的数据壁垒,优化生产、质量、物料、设备等全业务流程,提高生产柔性、缩短交付周期、优化物流效率,帮助企业迅速响应用户需求。
“对于企业生产来说,这个平台最大的功能,就是实现合同订单的可视化管理。一个合同项目,从签合同一直到交付给用户,整个过程都能可见和可追溯。”李计朝说,平台还有一个重要功能,就是成本预警和即时管理,也就是在生产过程中,如果发现问题,能够及时分级预警,实现快速处理。
在李计朝看来,科林电气各生产模块已经逐步实现自动化,未来要解决的问题,就是如何将自动化设备和信息化软件进行深度融合,最终完成数字化车间的组建。
数字化不仅仅是一种技术上的革新,更是一种工作方式的转变。数字化车间将机器和软件进行整合,很多操作和决策可以由电脑和自动化设备完成,实现了资源调度的灵活性、生产流程的可视性、质量控制的精准性以及生产数据的可追溯性,从而提升产品的交付速度和生产质量。
数据的高效协同,让车间变得越来越“聪明”。在企业数字转型的大趋势下,新一轮的变革,正从车间开始。
文/图 记者刘艳惠